Advanced Hotwire TIG Process for Weld Overlay: Revolutionizing Pipeline Protection
In industries where pipeline integrity is critical, such as oil and gas, petro-chemical, and power generation, the demand for reliable and cost-effective solutions to combat wear, corrosion, and high-temperature degradation is ever-growing. One such solution that has proven highly effective is the Weld Overlay process. Among the various welding techniques available, the Hotwire TIG process stands out as a next-generation method, providing significant advantages in terms of precision, efficiency, and performance. As a leading manufacturer of Automatic Weld Overlay Systems, we recognize the importance of continually advancing our technology to meet the rigorous demands of modern industrial applications. The integration of Hotwire TIG in automated weld overlay systems marks a significant leap forward in enhancing both the quality and productivity of the process.
What is Hotwire TIG?
The Hotwire TIG (Tungsten Inert Gas) process is an advanced welding tech-nique that incorporates a preheated filler wire into the standard TIG process. This preheating allows the filler material to melt at a lower arc energy, leading to more efficient deposition, reduced heat input, and a higher quality weld overlay. In this process, an electric current heats the filler wire as it is fed into the weld pool, enhancing the melting rate and improving deposition efficiency
compared to traditional TIG welding. By utilizing automated hotwire TIG welding systems, the process achieves precise control over the welding parameters, ensuring consistent results, particularly when applied to complex geometries or large-scale projects.
Key Benefits of Hotwire TIG in Weld Overlay Applications
Higher Deposition Rates
The introduction of hotwire preheating significantly increases the deposition rate compared to conventional TIG welding. This allows for faster overlay application, improving productivity while maintai-ning a high-quality weld.
Lower Heat Input and Reduced Distortion
Hotwire TIG provides a more efficient use of energy, reducing the overall heat input into the substrate material. This results in minimized thermal distortion and a more controlled heat-affected zone, making it idea l for delicate or thin-walled structures.
Superior Weld Quality
The process enables smoother, defect-free overlays with fewer chances of porosity or inclusions. The controlled nature of the hotwire process ensures optimal fusion of the overlay material with the substrate, leading to a more durable and reliable protective layer.
Precision and Rpeatability
The integration of automated systems with hotwire TIG welding ensures precision and repeatability. Automation allows for precise control over parameters such as wire feed speed, travel speed, and arc length, ensuring uniform overlays even on complex pipe fittings or components.
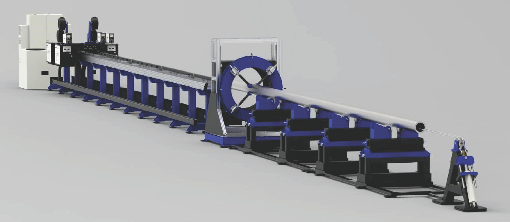
Cost Efficiency
The Hotwire TIG process offers a transformative approach to weld overlay, improving efficiency, quality, and performance across a variety of industrial applications. As manufacturers of automatic weld overlay systems, we are proud to offer cutting-edge technology that not only addresses the challenges of today’s demanding industries but also provides a reliable, long-term solution for pipeline protection.

Our automated systems, integrated with the advanced hotwire TIG technique, enable faster, more cost-effective, and higher-quality weld overlays, ensuring enhanced durability and reduced operational downtime. As the industry continues to evolve, the future of weld overlay technology will undoubtedly be shaped by innovations like hotwire TIG, offering new possibilities for perfor-mance, safety, and cost management in critical infrastructure.
Weldmatix Fusion Pvt. Ltd.
Web : www.clangrp.com