Role of Orbital Welding System in Semiconductor industries
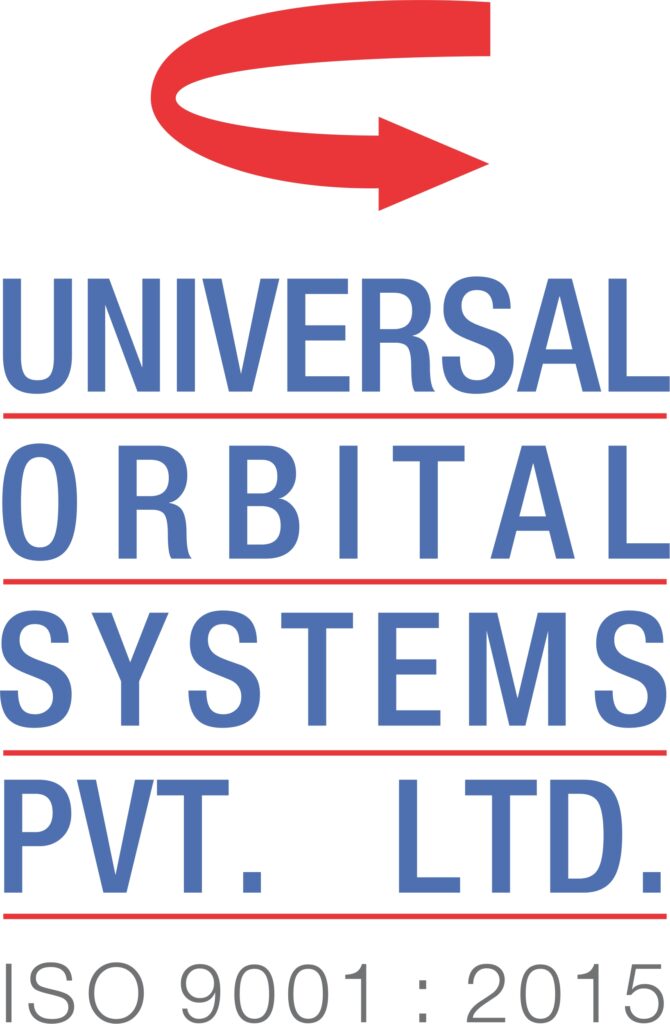
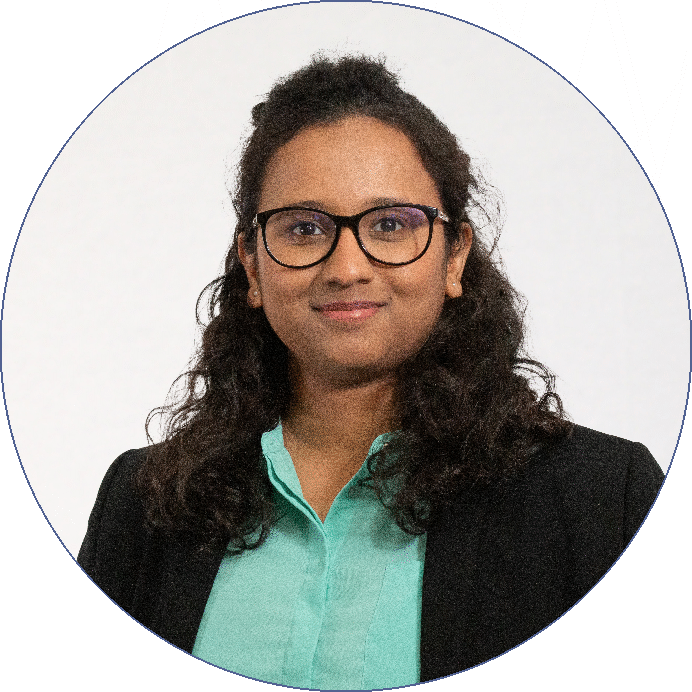
MSC Welding Engineering, Cranfield University
Universal Orbital Systems Private Limited
What are the welding requirements for Semiconductor industries and how does orbital welding plays role?
Semiconductar gas distribution system uses ultra-high purity (UHP) gases thus are transported through stainless steel tubes Controlling contamination is critical. Any disruption to the electron polished surface layer during welding can introduor impurities like manganese into the weld and heat-affected zone (HAZ). The industrial tolerances for contamination is in parts per billion, which means that the welding parameters are to be controlled at a ver stringent level as well as the welding requirements such as gas purity, gas flow and gas pressure inside the tube should abo be controlled to avoid any contamination.
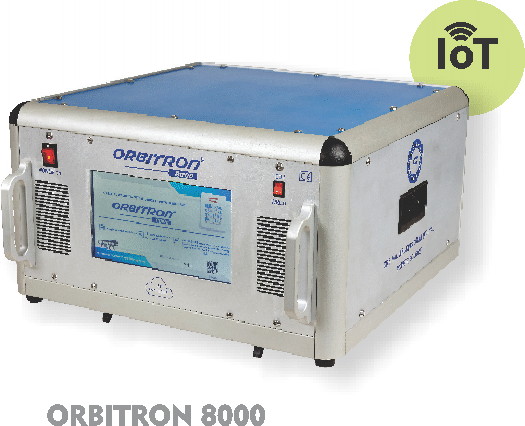
One of the major factors that are to be avoided in case of semiconductor pipeline welding is the inclusion of impurities such as manganese. Small amount of manganese is present in stainless steel and it is harmless at normal conditions and welding. However, in case of UHP semiconductor pipeline welding, even small traces of manganese can be catastrophic in nature. If the heat input is not optimised and purge gas flow is not regulated, manganese inclusion in the weld pool can occur. This inclusion can cause change in the chemistry of the grain boundary of the weld and make it susceptible to cracking. Uncontrolled and higher heat inputs can cause manganese inclusion in the weld joint that can cause change in delta/ ferrite, austenitic balance in stainless steel. This can affect mechanical stability by increasing brittleness in cryogenic or thermal-cycling conditions which is common to semiconductor industry.
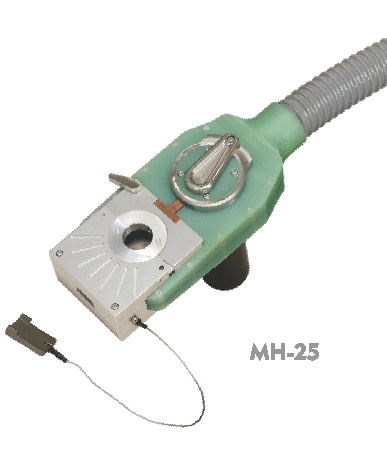
In order to meet these stringent requirements, orbital GTAW process becomes the ideal solution. The heat input and gas flow can be regulated as per the sector (tube sector) in case of orbital welding. The orbital weld heads are specially designed to accommodate micro-fittings that are common in the semiconductor industry. Universal Orbital has developed solution catering to the semiconductor industry with the user friendly interface. Such approach helps to get a very quality weld joints with the ease of equipment handling and better understanding of the application.
How do Universal Orbital Systems provide a solution to the semiconductor Industrial welding?
Universal Orbital has launched the new power source Orbitron 8000 Universal Orbital has a unique solution to enhance the welding quality of the micro-fittings that are used in the industry. Segment wise programming is provided with degree positional reference to optimize the welding parameters during welding. Orbitron 8000 is equipped with IOT connectivity to monitor the orbital welding process from any location. Documents of previous welds can be generated and stored on cloud as well as in the power source for analysis. The GTAW power source is tuned with highly stable current ensuring a precise control over the heat input thus providing accurate solution to the semiconductor Industry.
We have developed a new micro-weld head series which is specifically designed to accommodate micro-fitting. The weld heads can accommodate joints having straight distance of 12.7mm that is 5.35mm from one side. The weld head series includes MH-12 MH-16X and ΜΗ-25 Χ. These weld heads have detachable clamping systems for easy clamping of weld heads to micro-fittings and micro-pipelines. The weld head design is compact to accommodate complicated joints minimum straight portion of 6mm. All the fixturing blocks have centering gauges for accurate positioning of the joints.
Our company has developed Auto gas purge control unit that senses the pressure inside the tube and maintains the pressure inside the tube by adjusting the gas flow. This is a novel development by our company which was orchestrated keeping in consideration of the purge gas control and its effect on the weld quality. The precise control over the purging gas is also achievable as per the tube sector (0-360°). The auto purge control is essential to have a uniform weld quality over the tube in 5G position. This accurate control over the purge gas flow accounts for the high quality weld joints. The weld geometry is maintained due to such control and the control over purge gas flow contributes to a complete inert atmosphere with sufficient gas pressure thus avoiding any manganese inclusions. The control over heat input also contributes to keeping the weld pool temperatures that do not lead to manganese and other impurity inclusions.
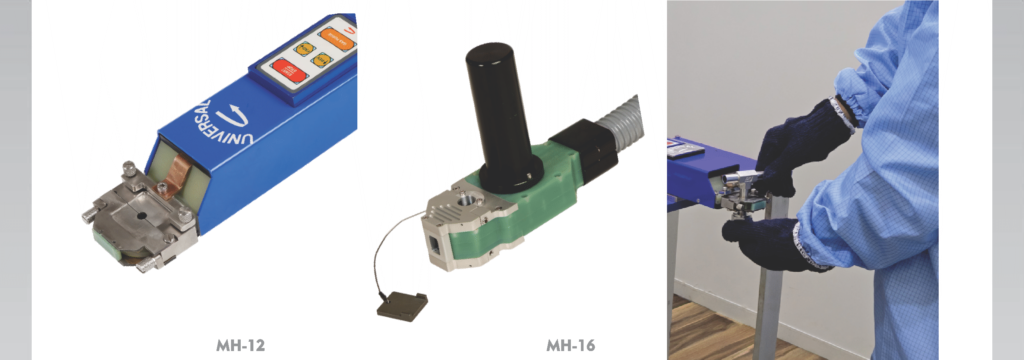
What is the future scope for semiconductor industrial welding and how have you equipped yourself as a company?
The advancements in technology will result in the setting up of more semiconductor industries to meet the needs. Semiconductor industry as an advancing future which implies that the semiconductor industrial welding requirements will also have such advancing demands. Orbital welding plays a very pivotal role in the expansion of semiconductor industry. As the only Indian orbital welding machines manufacturers, we have taken it as a responsibility to cater to the industrial need and deliver the best solution. This goes without a saying that our novel development of Auto purge gas control unit will add value to the enhancement and high quality weld joints. Our flexibility with our weld head and power source designs with continuous development sets us apart from others and we believe in providing a solution as per the customer demand.
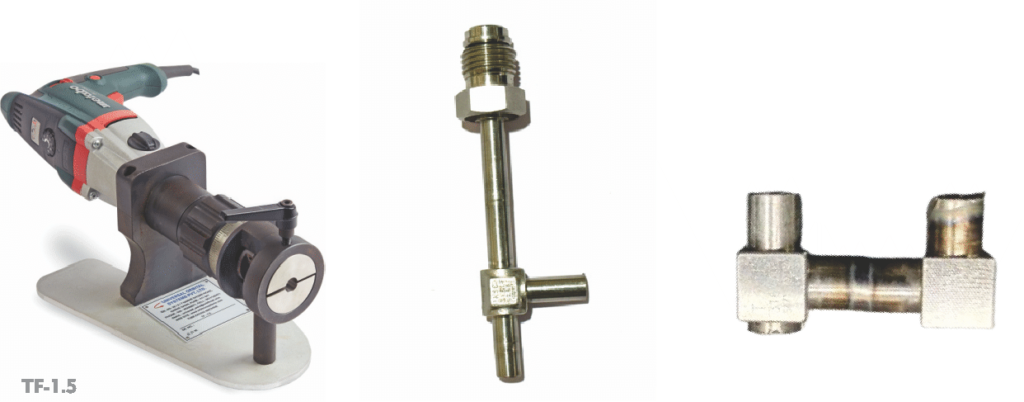
We have set up a clean room at our facility for trials of orbital welding of actual micro fittings samples. We have expanded our production capacities and introduced high precision VMC machines and CNC machines for accurate and indigenous manufacturing of parts. We have also conducted macro analysis, radiographic tests on the welded micro-fittings proving the quality of weld joints that is required in semiconductor industries.
As the only Indian manufacturers of orbital welding, we proudly say that we can contribute to the semiconductor industrial orbital welding by being an import substitute. We have prepared ourselves to fuel the development of semiconductor industrial welding and provide a complete orbital welding solution.
Universal Orbital Systems Private Limited
Web : www.orbitronsystems.com