Better to go contactless: The safety of machinery in intralogistics
Yellow is the colour of many safety switchgear devices in intralogistics. The con-tactless protective devices used in intralogistics include safety light curtains, multiple-beam safety light barriers and safety laser scanners. They offer specific benefits in this area of application, including greater flexibility. New series will open up additional applications.

Extensive automated and interlinked systems and conveyor lines are typical infrastructure in intralogistics. The ‘traditional’ way to safeguard danger points and areas – with fixed guards or ‘protective fences’ – is always the first solution chosen for several reasons. In conveyor lines or areas that require intervention, such as in pallet loading and unloading, contactless protective devices are use to boost productivity, as intervention can be accomplished much more easily. Contactless protective devices offer greater flexibility and use of space as they do not create a spatial barrier. They also make it possible to differentiate between man and material.
Contactless protective devices in place of protective fences
This is why contactless protective devices have been successful in getting a foothold in this (expansive) area of the safety of machinery. Specifically, this includes multiple-beam safety light barriers and safety light curtains.
Access protection and detection of individual body parts
Multiple-beam safety light barriers secure danger points and areas, e.g. on packaging and palletising systems. Multiple-beam safety light barriers with a typical beam distance of 300 to 500 mm are used to safeguard access areas with high safety clearances.
In comparison, multiple-beam safety light curtains have a significantly higher resolution of less than 40 mm. They are used when the safety clearance becomes smaller and parts of the body, such as hands and fingers, need to be detected. This makes them suitable for safeguarding areas such as hand-insertion points and transfer points. The resolution required for the detection of individual parts of the body is standardised in DIN EN ISO 13855.
Additional functions: blanking and muting
What makes contactless protective devices so appealing for intralogistics applications are additional functions such as muting and blanking. With the SLC series of safety light curtains from Schmersal, the user can blank selected areas of the protective field. Blanking means hiding fixed solid objects. As an example, a safety light curtain and blanking function can be used to safeguard areas above and below a conveyor belt. The conveyor belt is blanked, which means that only one safety light curtain is needed, rather than two, for a more efficient solution.

danger points and areas, e.g. on packaging and palletising systems.
The muting function works in a similar way, with additional muting sensors detecting the approach of transported goods and effectively muting the protective device. The benefit: transported goods can pass the danger point or can be removed from the system while an intervention by the operator is detected and the system is stopped. The extension of the MCU-02 module, which can be configured without software, makes decentralised muting a possibility. The muting sensors and the light curtain can be connected to the module with M12 connectors, significantly reducing the wiring effort required.
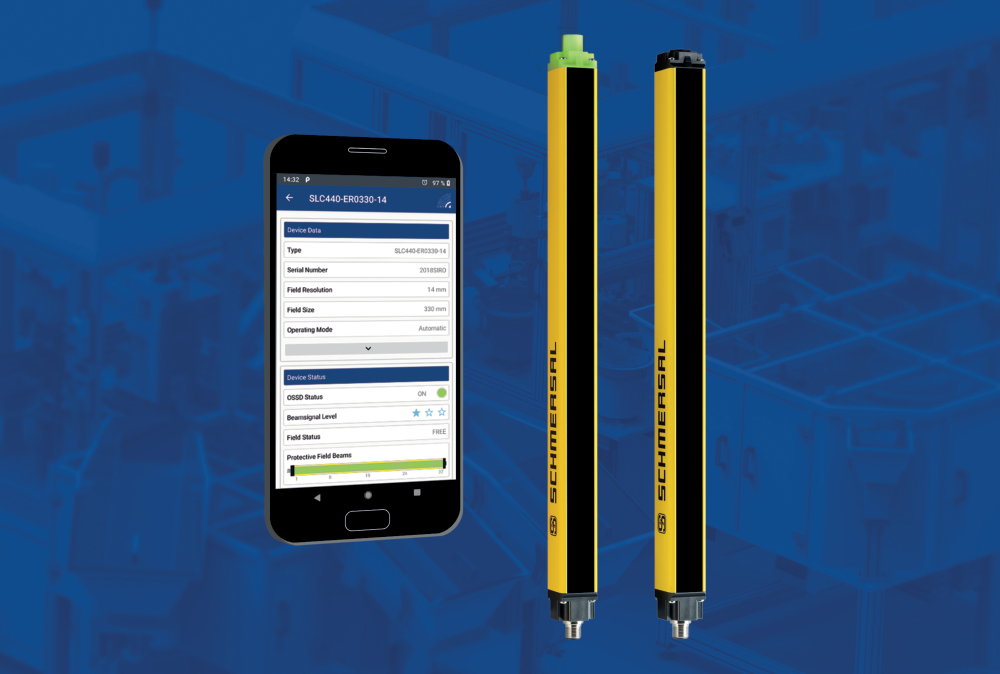
The best thing: additional diagnosis
In addition, safety light curtains and multiple-beam safety light barriers from Schmersal can also be equipped with options for higher-level diagnosis. This includes communication via a Bluetooth LE interface. The user can conveniently check the status of the protective device in the ‘SLC Assist’ app and retrieve a status message and diagnosis information, helping to accelerate troubleshooting and boost productivity.
The app also helps to save valuable time during commissioning: during alignment, information about the beam strength can be checked with ease on a smartphone or tablet. The new version of the app now also includes a function for determining the safety clearance to the danger area in accordance with EN ISO 13855. The clearance should be defined before assembly and checked at regular intervals during ongoing operation.
New: safety light curtains and multiple-beam safety light barriers with increased range
New to Schmersal’s range of optoelectronic protective devices are safety light curtains (SLC) and multiple-beam safety light barriers (SLG) with an increased range of up to 30 and 60 metres respectively. They offer reliable hand or body protection and enable monitoring over larger distances with minimal installation effort.
The increased range can be useful in a number of areas, such as when monitoring extensive packaging systems. Contactless safeguarding of conveyor lines up to 60 metres long is also a possibility – as an optoelectronic alternative to pull-wire emergency stop switches, which Schmersal also has in its range. With the help of deflecting mirrors, entire areas can also be safeguard and monitored with just one safety light curtain or multiple-beam safety light barrier. This reduces both the installation effort and the acquisition costs.
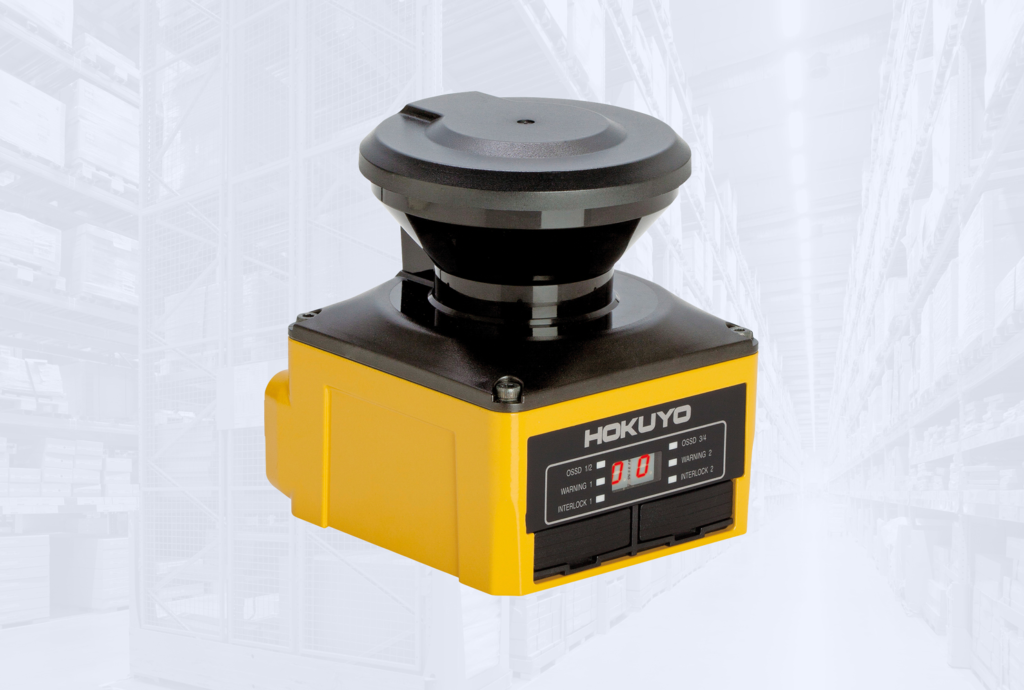
Laser scanner: compact design, large protection field
One of the present trends in intralogistics is the rapidly increasing use of collaborative robots (cobots) that can work with the operator without a safety fence being in place. Another growth market is automated guided vehicles (AGVs) and autonomous mobile robots (AMRs).
The use of safety laser scanners from the UAM series is ideal for safety-related environment detection in these applications. They can also be used universally as in spite of their compact design, they offer a high protective field range. The simultaneous protective field evaluation and the encoder inputs are additional reasons for their use in the safeguarding of stationary and mobile applications, i.e. for AGVs and cobots. These safety light curtains have proven themselves a reliable, safe and flexible solution at transfer stations from stationary conveyor technology to AGVs, and vice versa.
The protective device as a data provider
Another reason for using the latest generation of optoelectronic protective device in intralogistics is ‘integrated
intelligence’. The enhanced diagnosis functions can provide a wide range of operating data – fully in alignment with Industry 4.0. In addition, permanent monitoring can be used to spot irregularities for predictive maintenance and initiate service measures early on, before an unscheduled system shutdown. This helps to increase the reliability of production in the internal material flow.
Author:
Marcel Bogusch, industry manager for intralogistics at K.A. Schmersal GmbH & Co. KG, Wuppertal
Schmersal India Pvt Ltd
Email : info@schmersal.com
Web : www.schmersal.com