Leak B-TRACER at IMTEX 2025
Marposs proposes Leak B-TRACER: A Next-Generation Solution for Leak Testing Battery Cells
In response to the growing demands of the E-Mobility market, Marposs is proud to own the Leak B-TRACER, a revolutionary semi-automatic station designed for comprehensive leak testing of lithiumion battery cells.
Ensuring Safety and Performance in Next-Generation Batteries
The E-Mobility revolution depends on the safety and reliability of lithiumion batteries, a cornerstone technology in electric vehicles. These batteries often contain electrolytes with flammable components that can pose safety risks if compromised. Leakage can also lead to performance degradation. The Leak B-TRACER addresses these concerns by offering leak detection throughout the battery assembly process.
Two-Step Leak Detection for Unmatched Reliability
The Leak B-TRACER employs a two-step process to guarantee the integrity of battery cell seals
Pre-filling Leak Detection:
Before electrolyte filling and sealing, the Leak B-TRACER utilizes a proven helium leak detection method within a vacuum chamber. Helium gas is introduced into the empty cell, and a mass spectrometer precisely identifies and measures any leaks.
Electrolyte Tracing for Post-Filling Inspection:
Marposs has pioneered a ground-breaking Electrolyte Tracing technique for leak detection after electrolyte filling and sealing. In the event of a leak, the Leak B-TRACER vaporizes and extracts the electrolytes within the vacuum chamber, allowing a specially calibrated mass spectrometer to quantify the leak rate.
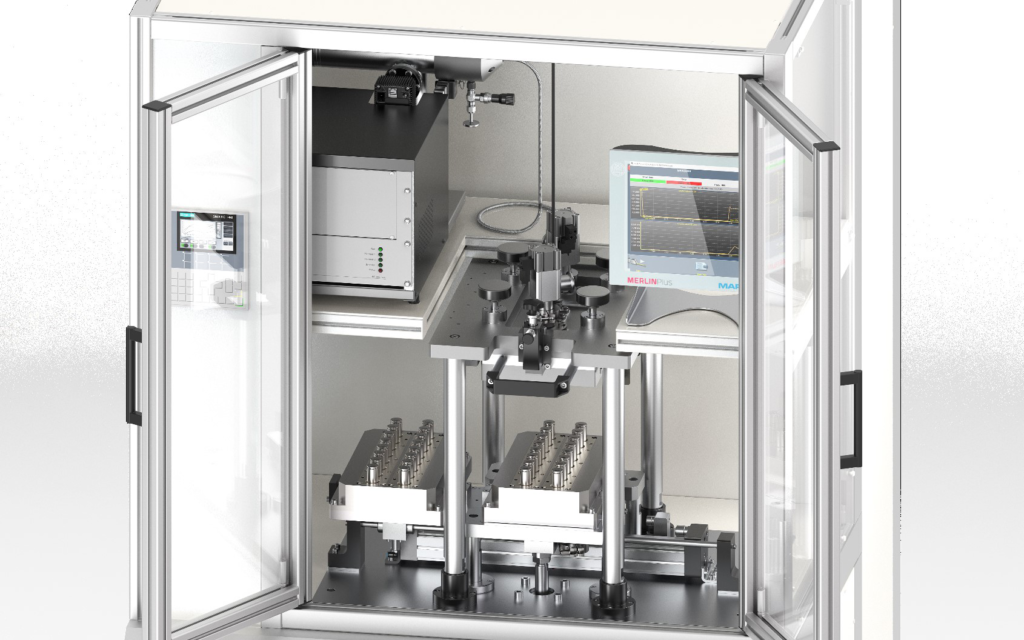
Flexibility and Efficiency for Seamless Integration
The Leak B-TRACER is designed for seamless integration into existing production lines. This user-friendly, semi- automatic station features manual loading with an automated testing cycle, making it ideal for:
- Prototype and pilot line testing
- Random off-line testing and statistical process control (SPC) analysis
- Re-checking of scrap batches
- Unmatched Versatility for Diverse Battery Applications
The Leak B-TRACER offers unparalleled versatility, accommodating various battery cell formats (button, cylindrical, prismatic, or pouch) and electrolyte types (DMC, EMC, PP, etc.). Furthermore, the system is adaptable for integration at different stages of the battery building process, including pre- and post-formation, as well as end-of-line testing.
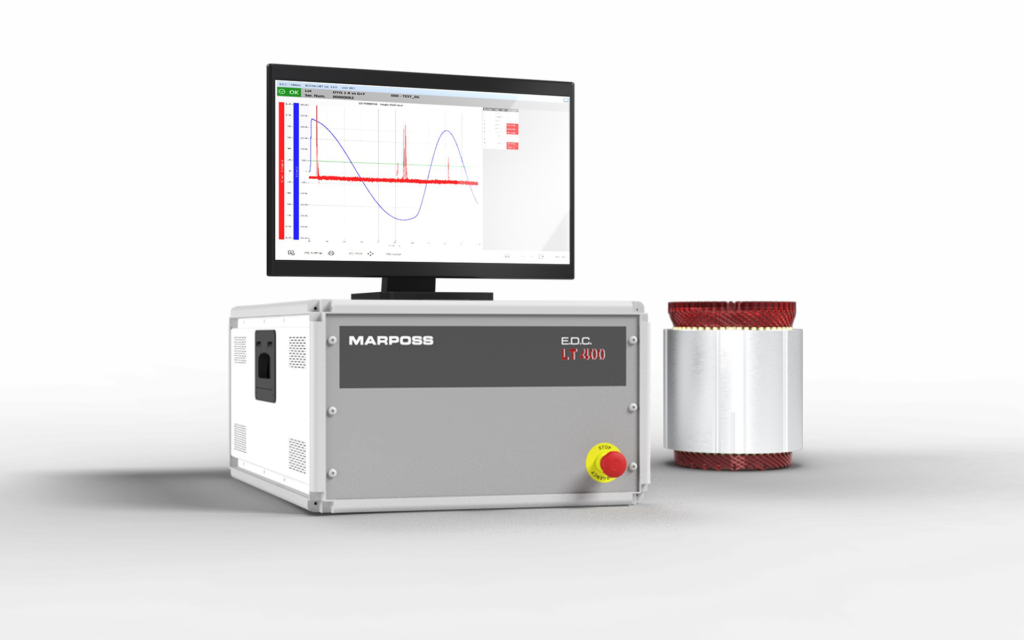
Fast Retooling and Easy Use
The Leak B-TRACER prioritizes ease of use with a rapid retooling kit, ensuring minimal downtime during production line changeovers.
Marposs: Committed to the Future of E-Mobility
The Leak B-TRACER represents Marposs’ unwavering dedication to advancing E-Mobility by providing innovative solutions that ensure battery safety and performance.
LT400: Winding and Insulation Analyzer
The rapid deployment of electric vehicles on a large scale is placing higher expectations on component reliability on manufacturers. These demands have implications for quality and process control requirements in the production line.
The insulation system of electrical machines is a critical reliability feature, as a failure of the insulation can lead to system failure. Standard electrical tests, required by regulations, are not sufficient to identify all types of failures because many faults produce only partial discharges, and these can only be identified by the partial discharge test method.
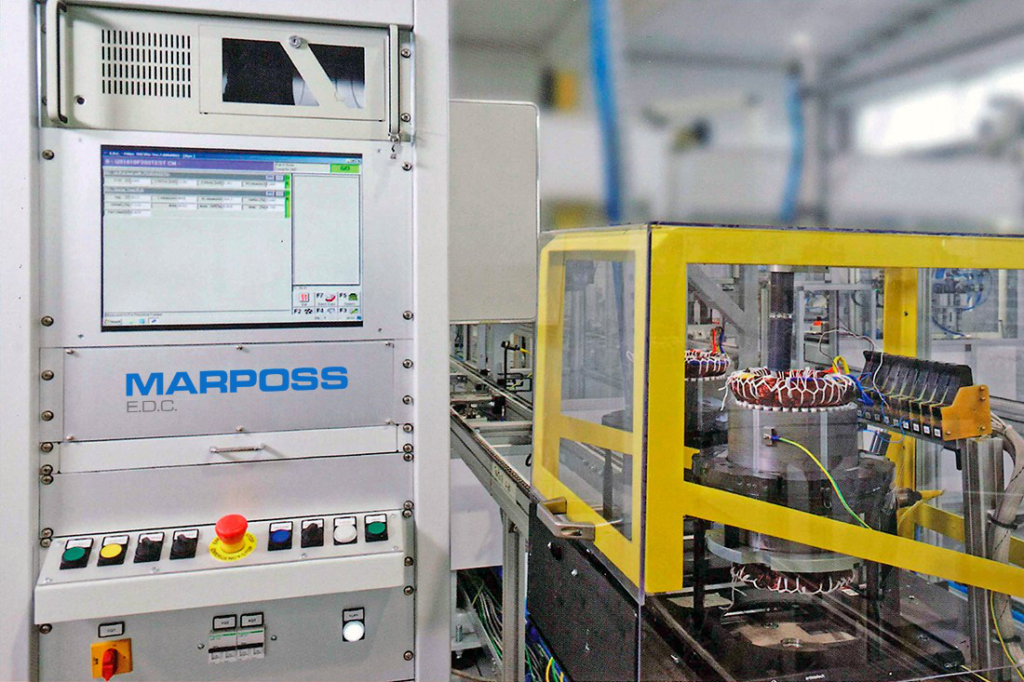
The LT400, a partial discharge winding analyzer for the R&D and quality control department, is a Marposs solution to identify all latent defects in the insulation system that could lead to failures.
A single unit capable of performing standard high voltage tests (AC/DC and Pulse) plus partial discharge measurements that allows to: select wires, plastic insulating materials, impregnation process; identify insulation weak points inside stators; identify the beginning of permanent insulation degradation during life tests.
The LT400 partial discharge measurement system is based on capacitor coupling technology. Compared to the antenna type solutions normally applied in this market, the capacitor coupling technique is more sophisticated and less sensitive to external noise and therefore more suitable for applications in the production area. Since it does not use an external sensor, the capacitor coupling approach requires equipment that can detect partial discharge simply by connecting the terminals of the product under test with the same cables used to perform standard tests. The result is a solution that is very easy to use (without any external sensors) and optimized for the production environment.
The LT400 uses the same flexible test software (developed in-house) as the production machines. This means that the calibration of the test parameters, optimized during the development of the device in the laboratory, can be fully transferred to the production test machines.
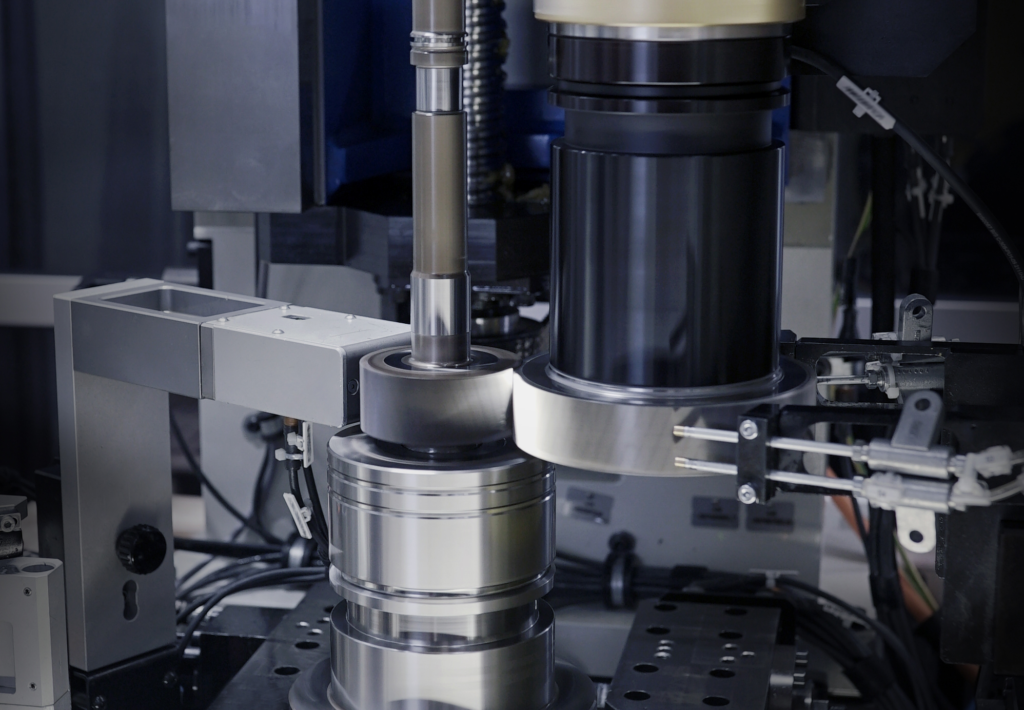
NVH G-EAR
Noise Testing Of Individual Gears
The IMTEX 2025 will offer its scene to Marposs presenting one of its most valuable application for the gear measurement and testing: the NVH G-EAR machine.
With the now firmly established hybrid (HEV) and full electric vehicles (EV), the noise of the drivetrain has become one of the major issues that every car manufacturer has to deal with. In BEVs, a silent gearbox not only ensures the mechanical reliability and efficiency of the electric drive unit, but also represents a comfort issue for the driver.
To achieve the target of a silent gearbox, it is paramount to test 100% each individual gear prior to the assembly of the transmission or gear reducer. The identification of potential noisy gears at this stage represents a huge time and cost saving for our customers.
The ideal solution for gear noise testing in a manufacturing environment is Marposs NVH G-EAR, a machine that is capable to test the parts at challenging operating conditions (3000 rpm rotation speed, 40 Nm torque) using a special master gear that engages the part based on the Single Flank rolling action. Marposs introduces Ultra-Wideband technology No interference for optimal process quality In recent years, there has been an exponential increase in Wi-Fi devices within production plants, not only smartphones, tablets and modems, but also automatic elevators and other material handling systems. This leads to saturation of the 2.4 GHz band with the inevitable presence of noise and interference, affecting the reliability of wireless probing systems, causing on the Single Flank rolling action.
Marposs introduces Ultra-Wideband technology
No interference for optimal process quality
In recent years, there has been an exponential increase in Wi-Fi devices within production plants, not only smartphones, tablets and modems, but also automatic elevators and other material handling systems. This leads to saturation of the 2.4 GHz band with the inevitable presence of noise and
interference, affecting the reliability of wireless probing systems, causing downtime and, more generally, decreasing the quality of the production process.
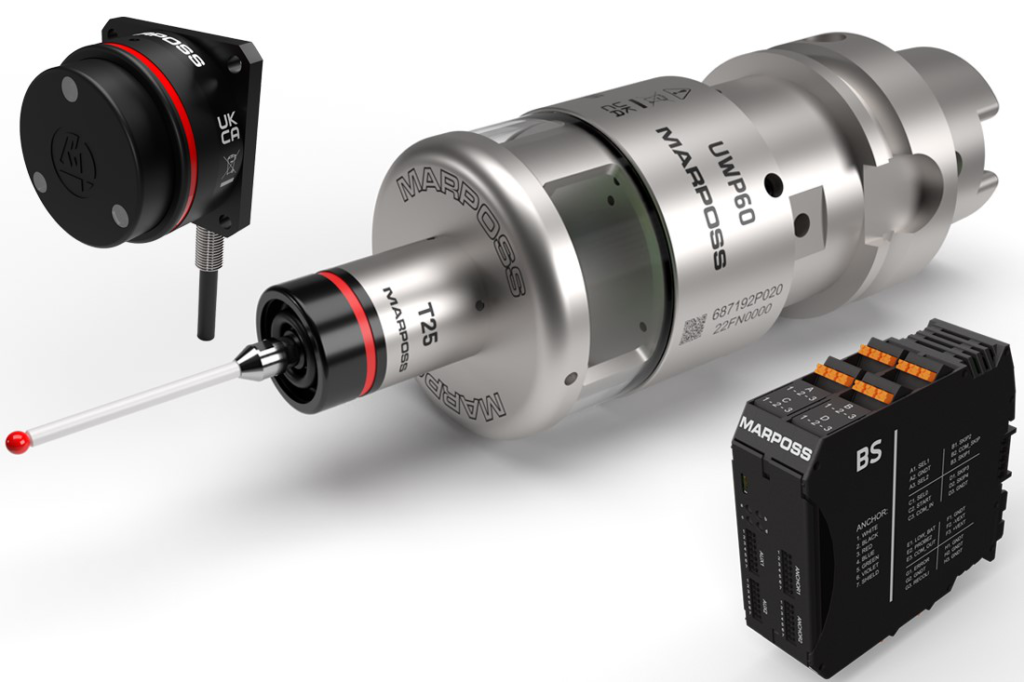
Marposs, always looking for new technologies to meet the growing market demands, can offer something more. Marposs Ultra Probing System is the new touch probing system with Ultra-Wideband technology, a real revolution for the machine tool industry. Thanks to the Ultra-Wideband technology, Marposs can place itself at a higher level of transmission than the standard, offering a new solution unmatched in terms of performance and reliability.
The most important feature, which is the main advantage introduced by the Marposs Ultra Probing system, is the use of a different transmission range: in Ultra Wideband, no other physical signal can interfere with the Marposs device, which means no interference and no machine downtime.
In addition, the system also features many improvements in its design. The anchor is the receiving antenna with an ultra-compact design that makes installation easier and faster. It also has 3 LED indicators. The anchor is connected to the machine’s CNC by a wired cable. In all systems, the connection is a weak point due to the sealing in a wet area which depends on proper mounting and then directly on the ability of the operator. Marposs Ultra Probing System introduces a new generation of wireless connectors with an extreme level of sealing due to its design, which does not depend on external operations.
In addition, the new Marposs APP – which allows system setup and real-time monitoring, combined with diagnostic and service operations – makes the system fast and easy to use.
Web : www.marposs.com